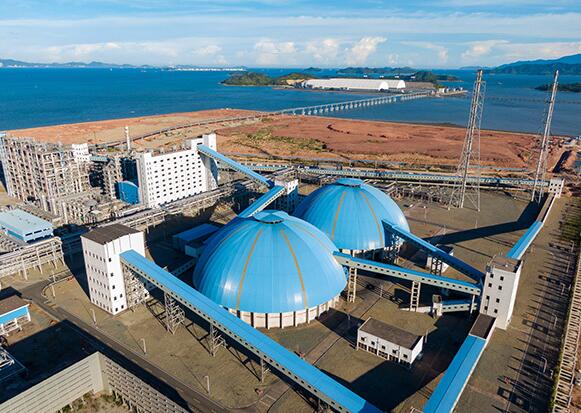
业内人士认为,推动煤炭清洁高效利用,要通过低碳化技术创新实现用煤少排碳、不排碳,加快煤炭由燃料向原料转变,突出煤炭的原料属性与多元高效利用。
作为实现煤炭资源有效利用的重要途径之一,煤制氢是以煤炭为还原剂,水蒸气为氧化剂,在高温下将碳转化为一氧化碳和氢气为主的合成气,经过净化、一氧化碳转化、提纯等环节,生产出氢气和合成气。
“Gas煤制氢联合装具有碳转化率高、热利用效率高、耗氧少等特点。与传统天然气制氢工艺相比,可降低成本20%至25%。”中海炼化惠州石化煤制氢部副经理周建欣介绍,自2018年起,惠州石化自主开发组态气化炉全过程自动化控制系统,组织开展焦过滤器反吹阀、滤芯、碳回收设施等进口设备国产化攻关,引入光纤测温技术,开发总结出余热锅炉操作法和硫磺单元低负荷操作法,实现了E-Gas煤制氢联合装置在不同负荷下平稳运行。
目前氢气制取的主要来源与困境
目前,氢的制取产业主要有三种技术路线:一是以煤炭、天然气为代表的化石能源重整制氢;二是以焦炉煤气、氯碱尾气、丙烷脱氢为代表的工业副产气制氢,三是电解水制氢。
但煤制氢工艺二氧化碳排放量约是天然气制氢的4倍,天然气制氢受制于国内高原料成本,焦炉煤气制氢的关键在于杂质的净化和产品氢气中微量杂质的控制,生物质直接制氢和太阳能光催化分解水制氢等技术路线仍处于初级阶段。相比之下,目前氯碱副产制氢提纯成本低、难度小、纯度高等优势。
“轻烃裂解”是极具潜力的潜在氢源
除上述焦炉煤气、氯碱尾气两类工业副产氢气外,包括丙烷脱氢(PDH)和乙烷裂解在内的“轻烃裂解”副产氢气,也可作为燃料电池供氢的潜在来源。且轻烃的原料组分决定其氢气杂质含量远低于煤制氢和焦炉气制氢,氢气纯度相对较高,但也面临着更低成本、更高效率的技术问题。
亚化咨询数据显示,中国共有8个PDH项目投产、5个在建,还有多家企业PDH项目处于前期工作,其中有确切投产年份规划的有4个,17个PDH项目副产氢气37万吨/年。而齐翔腾达70万吨/丙烷脱氢项目若满产,每年将新增副产氢气约2.65万吨左右,约占预计总产量的7.16%。按每辆氢燃料电池车每天加注5公斤氢气计算,这些副产氢气每年可供约20万辆氢燃料电池车行驶。万联证券认为,轻烃裂解是极具潜力的潜在氢源。
目前来看国内可供选择的制氢途径较为多样,但各类型制氢路线的经济性尚不足以保障燃料电池汽车的大规模商业化,这是当前产业发展所面临的瓶颈。但背后的问题,本质上是技术的问题。且这种技术困境,既有传统制氢途径面临优化的问题,也需要运用新技术解决分解水制氢等技术路线的难题。如何破解?齐翔腾达与中科院青岛所达成的强强联合,提供了解决科技创新难题的“新范式”。
打通科技创新“最后一公里”:实现产业链和创新链精准对接
长期以来,在企业界与科技界有一个难题,我国研发支出在全球研发支出中的占比位列全球前列,但是世界级投入所带来的科技成果供给与社会需求还存着相当大的差距。表面上看,高校和科研院所的研发成果过于前沿,企业用不上;企业在生产过程中遇到的很多技术难题,高校和科研院所又不愿意去做。
但背后有一个很重要的问题,是“选择”的问题,是初始选择就不对,造成了科研成果转化的困境。而解决这个问题的结合点在于——需要选择既是产业未来发展需要,同时也是企业未来市场发展需要的“两结合”点。
齐翔腾达中科院青岛所合作的新能源等技术研发和产业化应用,就是这样的“结合点”,齐翔腾达恰恰能够提供市场供给,中科院青岛所能够提供技术支持,这是真正地打通了科技创新“最后一公里”,实现产业链和创新链精准对接。
公开资料显示,齐翔腾达现有的甲乙酮、低碳烷烃脱氢等生产装置都会副产氢气,目前每年产量在1-1.5万吨左右。随着今年底70万吨/年丙烷脱氢建成投产,齐翔腾达氢气产能将大幅提升,据测算每年将新增副产氢气约2.65万吨左右。
但工业燃料氢气中微量CO杂质的存在能够快速毒化燃料电池催化剂,开发出不含CO的氢气(CO≦0.2ppm)制备技术是氢能研究的重要方向。而近期,中科院青岛所与德国汉诺威大学的团队合作,开发出一种新型用于氢气提纯的高稳定性混合导体陶瓷膜,低纯氢气的燃烧可以促进陶瓷膜另一侧水分解所生成氧气的原位移除,从而直接获得不含CO的氢气,可作为燃料直接用于氢燃料电池。
氢能产业链在未来将发生重大变革
完善的氢能产业链包含:上游氢气制取、储运、加注;中游燃料电池及其核心零部件的制造;下游为燃料电池及氢气应用,涉及交通、工业能源、建筑等多领域。
预计到2050年,氢能产业链上下游均有重大变革。目前氢能产业链上游普遍通过化 石燃料制氢+高压气氢拖车形式进行氢气制取与储运,未来将向可再生能源电解水制 氢+液氢管运的形式转变;下游氢能目前主要应用在工业领域,包含炼化、合成氨、甲醇生产等,未来将在工业、交通、建筑、储能等多领域进行全方位的应用,特别是 在交通领域,氢气高能量密度的特性使其在航空、船运、重卡等领域颇具应用潜力, 交通领域的氢气需求有望从 2018 年的不及 1 万吨增长至 2050 年的 2.96 亿吨;而目 前看,氢燃料电池车是技术最成熟、未来最具潜力的下游应用方向,其也将带动中游 燃料电池及相关零部件市场规模增幅快速提高。(报告来源:未来智库)
从投融资角度看,2020年氢能产业链上游投融资规模为 712 亿元,其中制氢领域项 目投资环节多,设备投资大、投资周期长,是上游投融资规模中占比最高的环节,达 95%;中下游燃料电池及汽车领域 2020 年投融资规模为 515.2 亿元,较 2021 年同比 增长 78.5%,燃料电池汽车、系统、电堆是目前投资重点环节,合计占比达 91%,未 来短期内系统、电堆、膜电极、双极板、空压机将会是投融资重点环节,而质子交换 膜、催化剂、碳纸等环节仍面临较大的资金缺口,短期内发展受阻。
灰氢在未来将被逐渐替代,蓝氢成为过渡解决方案
从制取原理看,制氢方式大体可分为四类,化石能源制氢、工业副产制氢、高温分解 制氢、电解水制氢,以及光解水、生物质等技术尚不成熟的其他制氢方式。化石能源、 工业副产及高温分解制氢由于在生产氢气的过程中排放大量 CO2,由其所制氢气也 被定义为灰氢;在制灰氢过程中结合碳捕集、利用及封存技术(CCUS)减少碳排放 后所得氢气被称为蓝氢;而通过可再生能源电解水所制氢气被称为绿氢,其制氢过程中几乎没有碳排放。
目前化石能源制氢仍是全球包括中国在内的主流制氢方式。全球制氢量最高的工艺 路线是天然气制氢,占全球制氢量的 48%;煤制氢产量占比约为 18%,主要来源于 中国的煤制氢(ETC)。中国“富煤缺油少气”的能源禀赋致使煤制氢路线产氢量在 国内占比最高,2019 年达到 63.54%,其次是工业副产氢和天然气制氢,而电解水制 氢仅有微量示范应用。
未来电解水制氢将逐步对化石能源和工业副产制氢进行替代。中短期来看,中国氢气来源仍以化石能源制氢为主, 以工业副产氢作为补充,可再生能源制氢的占比将逐年升高。预计到 2050 年,约 70%左右的氢气由可再生能源电解水制取,其余 20%由化石能源制取,10%由生物制氢等 其他技术供给。
文章来源:未来智库,ipo观察,人民网
版权与免责声明:
1、本站所发布信息有原创信息、转载信息;
2、转载此文是出于传递更多信息之目的;
3、凡注明信息来源为其他机构和媒体的信息为本站转载信息,本站不对其观点的正确性和内容的真实性负责。若有来源标注错误或侵犯了您的合法权益,请作者于本平台发布一周内持权属证明与我们联系,我们将及时更正、删除,谢谢。